Coronavirus may have temporarily interrupted solar installation schedules, but one thing it didn’t touch was technology innovation and R&D. The summer of 2020 saw a number of solar panel manufacturers announce new models surpassing 500 W. With 350-W panels generally seen as amazingly powerful just three years ago, many companies are jumping to new extremes fairly quickly. The explanation for higher power classes comes down to a shift to larger crystalline silicon wafers.
A silicon wafer is the building block of a solar panel. Once wafers are doped with various chemicals and “electrified,” they become solar cells. Solar cells connected together become solar panels.
In the early 2000s, solar wafers were small, around 125 mm (5 in.) in length. In 2012, the M0 wafer (156 mm) was introduced with the M2 wafer (156.75 mm) eventually becoming the dominant size. Then came the M4 wafer (161.75 mm) around 2016, and the last few years have seen increased interest in even larger wafers with M6 (166 mm), M10 (182 mm) and G12/M12 (210 mm).
The bigger the wafer, the more power it can generate because of its larger surface area. Making wafers as big as possible would seem like the obvious path to take, but industry-adopted standard panel sizes add constraints to the equation.
A 72-cell Trina solar panel common in 2016 using M2 wafers averages about 6.5 ft long and 3 ft wide. It produces upwards of 380 W and weighs 50 lbs. Trina’s recently introduced Vertex module using G12 wafers averages 7 ft long and 3.5 ft wide – and only uses 50 cells. The power output increases to 500 W, and the larger panel weighs 65 lbs.
On paper, it’s not a huge difference in size or weight. In practice though, these larger modules exceed OSHA’s 50-lb weight limit for one-person installation. And large-format modules may prevent multiple rows from fitting on a small pitched roof. Using big-wafer modules in residential applications becomes a little more difficult now.
We talked with three major players in the U.S. residential market to see how they think the transition to bigger wafers will affect their businesses and plans for future products.
SunPower pushes to the limit with Maxeon spinoff
SunPower is one of the leading residential dealership models in the United States. Along with Panasonic, SunPower long supplied the residential market with 96-cell panels using 125-mm wafers. SunPower CEO Tom Werner said SunPower’s use of smaller wafers happened because of the company’s early start in the industry.
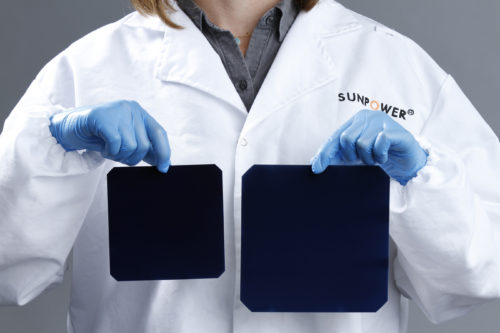
In 2019, SunPower jumped from 125-mm wafers (left) used in its X-series to M4-equivalent wafers (161.75 mm) for its A-series of modules (right). The new Performance 5 panels will use even larger wafers. Credit: Paul Sakuma Photography
“We designed our product in 2005 when polysilicon was expensive, so the benefit to go to a bigger wafer was outweighed by the price of polysilicon at the time,” he said.
But now things are starting to change. SunPower has officially split into two companies – SunPower will soon just focus on U.S. and Canadian residential and distributed-generation installations, while its spinoff Maxeon will continue producing solar panels. SunPower will exclusively sell Maxeon solar panels through its 1,000+ dealers. Meanwhile, Maxeon will sell its panels globally, with about 25% of its sales going to the United States.
Maxeon’s first order of business is transitioning to wafers that are as large as possible. The new Performance 5 panels will use the 210-mm G12 wafer. The decision to move into bigger wafers was because the costs finally penciled. Silicon isn’t as expensive as it was in 2005. Plus, Maxeon now has a strengthened relationship with Chinese silicon wafer supplier Tianjin Zhonghuan Semiconductor (TZS), which makes the scale to G12 wafers possible.
“From a supply chain perspective, TZS is part owner in our venture and is leading G12 wafer development,” said Jeff Waters, Maxeon Solar Technologies CEO. “We source those cells into our joint venture factory in China.”
Many things go into the decision to switch up the module manufacturing outcome. Werner said companies have to consider how larger modules will work with existing mounting systems, how design software will adapt to new dimensions and how installers will handle different module sizes. There are a lot more questions when it comes to specifically using large-format modules in the DG market.
“It’s certainly possible for larger-format panels to enter the residential market,” Werner said. “In DG, you lose some things as you get bigger panels. You have shading and chimneys. If you have a large-format panel, it’s likely less effective in those environments.”
So Maxeon will first focus its large-module efforts to the utility-scale market. Waters said Maxeon is working on R&D to drive down installation times and make G12 modules adaptable to the residential market. Panels could be lighter but still larger. Glass could be reduced so large-format panels can be hoisted onto a roof by one person.
And in a market that is concerned about aesthetics, Waters said there is still room for improvement before bringing G12s to the roof.
“As [larger] wafer technologies mature, you can get black colors and more color uniformity that would lend to the residential space,” Waters said.
LG is taking baby steps
LG is another residential powerhouse that is concerned about aesthetics. It’s one of the reasons it hasn’t strayed far from its full-size cell roots into half-cut or shingling technologies. LG was one of the first residential manufacturers to adopt the larger M4 wafer size in 2016, but it is approaching even larger wafers with caution.
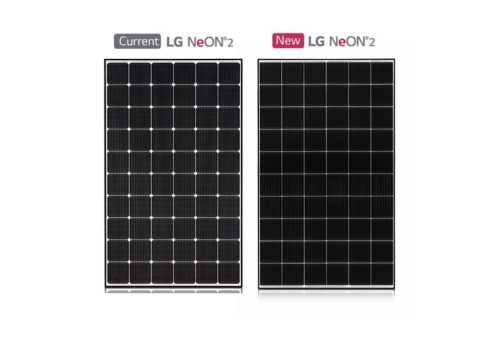
LG recently updated its wafer choice for the NeON 2 panels from the rounded M4 (left) to the more square M4+ (right).
LG announced in July 2020 that it improved the output by 15 W and efficiency by 0.4% on its NeON 2 line of panels by moving from M4 wafers to M4+. M4 wafers have rounded corners while M4+ wafers are full squares. No major manufacturing equipment changes were needed for this swap, and the new panel’s look isn’t too different. But LG is planning to transition to M6 wafers beginning in Q1 2021.
“M6 should be the limit for us,” said David Chang, senior director at LG Solar USA. “As you get larger than that, you start dealing with issues like microcracks, and color uniformity is hard. That’s a big concern of ours since we’re concerned with aesthetics.”
And if the manufacturer isn’t willing to use half-cut or shingling technology, microcracks could be more prevalent in larger full-size wafers. As wafers get bigger, they can warp and twist. Cutting the larger wafer into strips or even in half improves the structural integrity.
In general, it seems the industry will have to adapt to larger wafers, for better or worse. Traditional PERC modules have hit a wall when it comes to improved efficiency at smaller wafer sizes.
“Commercially, the industry has hit the limits [of improved efficiency],” Chang said. “For us, we have a back-contact, n-type technology and our cell efficiency is close to 25%, and it’s probably reached the max. That’s why module manufacturers have taken the approach of improving module technology, whether it’s half-cut or shingling or tiling, that improves efficiency by lowering resistance. We’ve done everything we can do on the cell side. The only way to get more output is to increase the wafer size.
“The prediction is that M6 should be the dominant size for the next couple years, then we’ll see,” Chang continued. “If it happens, we’ll standardize and shift to larger wafers.”
Panasonic feels fine where it’s at
Panasonic has stuck to its guns with its 96-cell modules using the small 125-mm wafer. But David Lopez, group sales manager for Panasonic Solar & Storage, said the writing is on the wall that the company will have to switch to larger wafers eventually. Panasonic is at the mercy of what wafer suppliers choose to make.
“There will be a point where everyone has to go to a bigger size, including us,” Lopez said. “We have been looking at it, but we’re going to be forced to do it.”
Panasonic has kept producing panels with 125-mm/5-in. wafers because that’s what its factories could support.
“Our latest factory in Malaysia was built in 2011,” Lopez said. “At that point, we were manufacturing 5-in. wafers in Japan. We adopted that size because we felt comfortable with it. We are a conservative company, and 5-in. was a size that gave us more reliability. We were one of the first to offer a 25-year warranty, that our panels won’t degrade [more than 10%] after 25 years. Keeping the wafers at 5 in. gave us that peace of mind.”
Panasonic feels it’s still in a good spot without larger wafers because it has been an innovator with heterojunction technology (HJT). While dominant PERC brands are reaching their limits on improved efficiency, HJT still has room to grow, so Panasonic can release more powerful modules in its same lines for years to come. But for companies instead choosing to go the bigger-is-better route, Lopez said he’s concerned about the mechanical attributes on these panels and keeping them under OSHA’s 50-lbs-per-one-installer limit for the residential market.
“If you look at the panels increasing size, in order to keep the weight below 50 lbs, they have to make the glass thinner,” he said. “Then you are reducing the wind loads, the snow loads and making microcracks likely to happen. Some are cannibalizing reliability by going to higher power.”
Panasonic is focused on quality and reliability, not necessarily flashy output numbers.
“Many of the panels released this year, they’re exactly the same efficiency as last year’s panel. They just made it bigger,” Lopez said. “You might save one microinverter or 4 in. of rail. The job doesn’t really add up on residential, but on utility-scale it does. The amount of power you put on the roof, if the efficiency doesn’t improve, it’s the same.”
The industry may see large-format modules in the utility-scale market within the next year, but manufacturers are waiting as the technology advances before placing all bets on big wafers on residential roofs.
Leave it to SunPower to always be striving for maximum efficiency! Maybe I missed it, but is there a theoretical maximum efficiency number?
It’s around 29% for your basic silicon solar cell.
These small efficiency gains are great – I wonder when we’ll see a huge jump in solar panel efficiency like 5-10% efficiency jump.