The use of non-curing butyl polymeric sealants was first introduced to the U.S. roofing industry more than 60 years ago and is now gaining traction in the solar industry as a sealant for roof attachments, providing strong weatherproofing capabilities and extended service life.
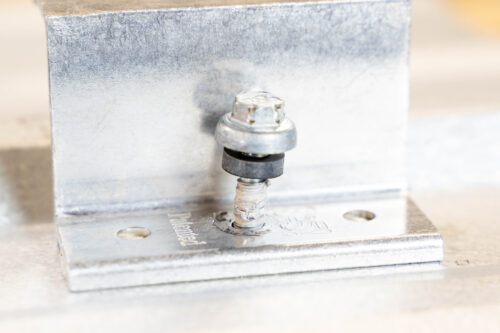
A threaded fastener driven through the butyl tape factory applied to S-5!’s VersaBracket metal roof attachment. S-5!
Butyl sealants are popular because they are easy to apply in either cold or hot temperatures. Non-curing butyl compounds have a sticky constitution — like chewing gum — that is retained throughout their service lives, even in extreme temperatures. These sealants are sustainable, non-toxic and environmentally friendly. They require little, if any, surface preparation — just clean any visible dirt and surface debris. The sealant “tacks” (clings) to threaded fasteners driven through it, providing additional secondary weather protection.
Although pump-able tube grades of butyl (72%± solids) are available, extruded tapes (98%± solids) are strongly preferred due to their manufactured dimensional consistency rather than the discretion of an individual squeezing a caulking gun and guessing how much is enough. Both over- or under-application can be detrimental to performance.
A service life study conducted by the Metal Construction Association was led by Rob Haddock, CEO and founder of solar mounting manufacturer S-5!, shows that brand-specific butyls still demonstrate exceptional elasticity, adhesion, cohesive tensile strength and webbing properties after 35 years of service. Based on lab studies of those specimens taken from 14 aged roofs, the same sealant chemistries are estimated to last 60-plus years.
Butyl formulations have changed, and many have improved over the years, but it is important to note that butyl polymers are not all created equal and there are no standards that control their composition. Isobutylene rubber is blended with isoprene and is typically below 20% of the formulation. (A higher rubber ratio does not mean a better sealant compound.) Ultraviolet (UV) inhibitors, insect and fungal repellants are often additives, but exact formulations are all proprietary trade secrets and vary widely.
A lab chemist who fully understands sealant types may run some tests for cone penetration, tensile strength and adhesion, but these tests are merely early life indicators. The only certain measure of aged performance of butyl polymer sealants is the documented history of brand-specific, long-term performance on real roofs over decades of time. Formulations that are not able to withstand the test of time can harden, lose adhesion or exhibit compound breakdown (de-polymerization) in a fraction of time when compared to their counterparts.

Webbing, elasticity and adhesion of butyl within a joint after 34
years of service. Rob Haddock, Metal Roof
Advisory Group
The butyl sealants that S-5! has been pre-applying to its metal roof attachments for 32 years, since the company’s inception, based on its founder’s experience and advised by specialized sealant chemists and examining brand-specific butyl performance not only in the lab, but on thousands of roofs and over decades.
It is critical to use only supply-side sources for butyl that have a minimum of 40 years’ empirically proven history to ensure proper performance. Developing the right product design to pre-apply the sealant is equally important as sourcing a proven butyl compound. Applying the right amount with the right geometry, while preventing over-compression and exposure to harmful UV are all critical design elements. All of S-5!’s attachments with pre-applied butyl have a reservoir to prevent over-compression, thinning and UV exposure, all of which can compromise butyl’s service life.
Next, to substantiate a proper design, it is also necessary to leak-test attachment products with pre-applied sealants in their specific application. The most demanding, but also the most applicable for roof attachments, is ASTM E2140, The Standard Test Method for Water Penetration, the static water test that Haddock helped to develop 40 years ago at ASTM.
Beyond choosing a butyl sealant with a history of reliable performance and designing attachments properly to pre-apply butyl tape, the following are some best practices when using sealants to leak-proof solar photovoltaic roof attachments:
Don’t use any sealant as a surface-applied fix on a roof. Surface applications are subject to degradation from UV, ozone, mechanical abrasion, dirt and other contamination. Butyl polymers are particularly vulnerable to UV exposure. If sealants are not properly protected, multiple factors can break down their chemical bonds. Application of butyl in gasket fashion will help protect the sealant from these threats. But even when applied as a gasket, the best sealants still have vulnerabilities. Look for attachments where the sealant is concealed from exposure and is minimally extruded at outward edges of the part when installed.
Avoid over-compression. Tighter is not better in this case. When you drive the screw, seat it, but do not over-torque it. Otherwise, you could thin and displace the gasket material, reducing its life and effectiveness. The best practice is to utilize a part design featuring a built-in recess to encapsulate the material and inhibit over-compression

Factory-applied butyl tape in the base of an S-5! SolarFoot metal roof attachment. Patrick Thompson/S-5!
Main takeaway
The growth of non-curing butyl polymers to seal roof attachments in the solar industry is a positive trend, as butyl is a sealant with long-lasting performance. Along with increased use comes the increased responsibility to use durable formulations from proven sources to match the lifetime of the solar and roof system. A best practice is to use pre-applied butyl to ensure the sealant works as designed and is never compromised during installation and for the service life of the entire solar and roof system. Learn more about butyl sealants in S-5!’s blog all about butyl.
S-5! is the top quality standard of metal roof attachments and should never be substituted with the imitations.